Tungsten Carbide Drawing Dies Making Process
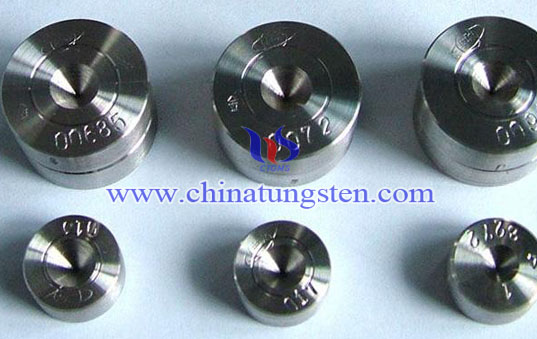
Tungsten carbide drawing dies making process divided into four steps:
1. die blanks processing
Tungsten carbide drawing dies cores in the sintering process will produce shrinkage, due to different batch ingredients, pressing and sintering processes are different, there are large differences in the amount of shrinkage; die blanks all parts vary the amount of shrinkage, tend to form "saddle "or" bell "shape. Fluctuations die blanks dimensions, although in line with standard die blanks, but far more than the suits mold inserts interference requirements, resulting in core when subjected to loading inserts prestressed serious uneven mold life significantly reduced, therefore, must die blanks be cylindrical grinding, grinding machine requires the use of special fixtures, grinding with a diamond wheel.
2. mounted inlaid amount of interference
get when loaded inserts to make certain prestressed core, die housing bore diameter smaller than the outer diameter of the core, called the difference between the amount of interference. The amount of interference according to core size and bias, drawing stress and casement method to determine. Table 1 shows the actual amount of interference mold inserts installed when. Mold suits inlaid with two hot method and cold method, cold method is too small amount of interference, pre-compressive stress obtained is small, used for manufacturing specifications small, soft metal used in drawing dies.
3. die sets processing
mold sets using lathe turning forming, machining control points are as follows:
(1) die sets must reach 0.80 an inner diameter of roughness I. 6 m, in favor of close cooperation with the die sets;
(2) die sets and die blanks to the outer diameter of the inner diameter of one to one, to ensure that each mold interference accurate;
(3) the bottom surface of the mold and the mold kit holes must be parallel to the outer end, and to ensure that the loading sleeve and die hole perpendicular to the centerline;
(4) the degree of mold kit oval hole should be as small as possible and should not be greater than 0.02 mm. When hot charging mode sets the outer surface of the car should be light, to ensure uniform cooling after loading inlay.
4. mounted inlay craft
cold-loaded inlay craft is blank mold at room temperature pressed into the mold with the press kit. Cold Act requires precise amount of interference on the mold core and sets require high dimensional accuracy, the advantage is no need for heating equipment, save energy, reduce costs.